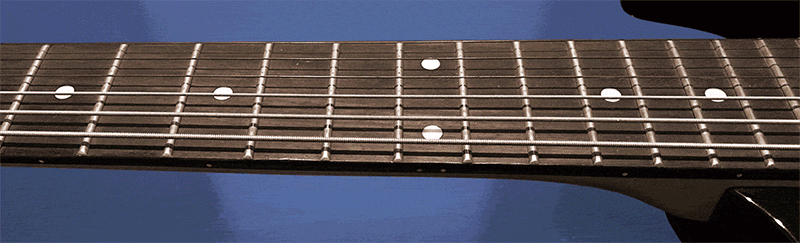
BEHIND THE SCENES
Design, Art, Data Management, Production, Manufacturing.
Design, Art, Data Management, Production, Manufacturing.
This concept works in both physical and digital form, but the physical version quickly crashes into realities that create a lot of limitations, and demands sacrifices in order to create something sensible. Yet, all the work put into making the limited physical version is extremely important for informing what can be done with a virtual version. Creating the same concept in VR or AR will be extremely liberating since many of the sacrifices made to create a physical version simply disappear, and the core functionality can be vastly extended.

Here is a final cut-out, in this case highlighting the Harmonic Minor scale in the Key of A, with the notes subdivided and grouped by the underlying chords.
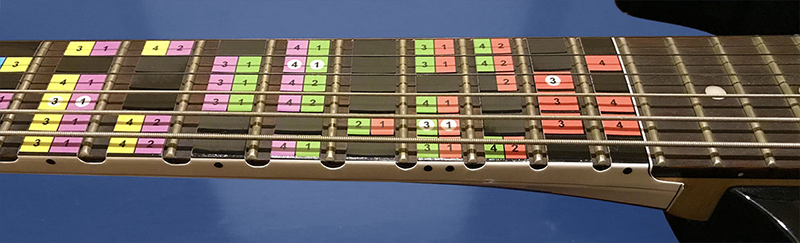
This is the same cut-out mounted to a guitar - snugly fitting under the strings and around the neck. The journey from concept to physical form involved a lot of data collection and prototyping to figure out how to make a single cutout that would fit a multitude of different popular guitars brands.
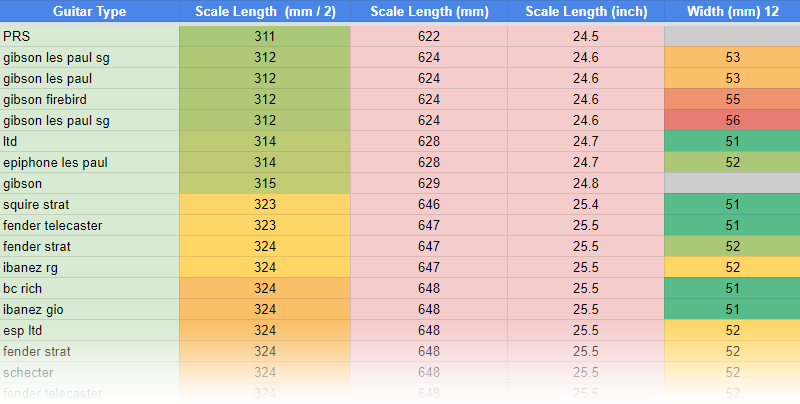
The first step from concept to physical reality was to figure out what size the cutouts should be. Millimeters quickly became very important, since there are a great multitude of small differences, depending upon guitar brands and models.
I searched online to gather guitar size specifications - but after doublechecking what I found, it soon became clear the information wasn't accurate enough to proceed with confidence. I needed to do my own hands-on research, so I went to the local music stores and measured over 30 different guitars, and tabulated my own data.
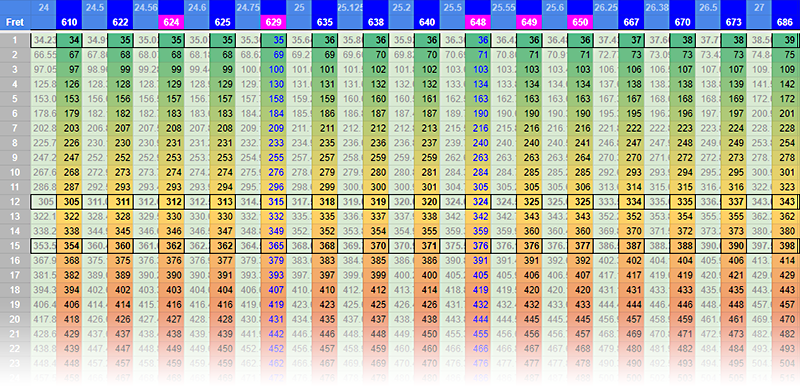
Due to the differences in so many guitars, I had to make some practical decisions for a range of popular models that I would support. Since the scale length (and therefore the distance between frets) varies per guitar, it wouldn't make sense to fit the design to perfectly fit only a few models. The solution was to create a single layout with built-in variance that would allow it to fit on many different models.

This was accomplished by identifying the min and max variance between my target models and adjusting the width of the cut-out areas for the frets, to gradually narrow from one end of the pattern to the other. The end-user never needs to notice this or even be aware of it - it just works.
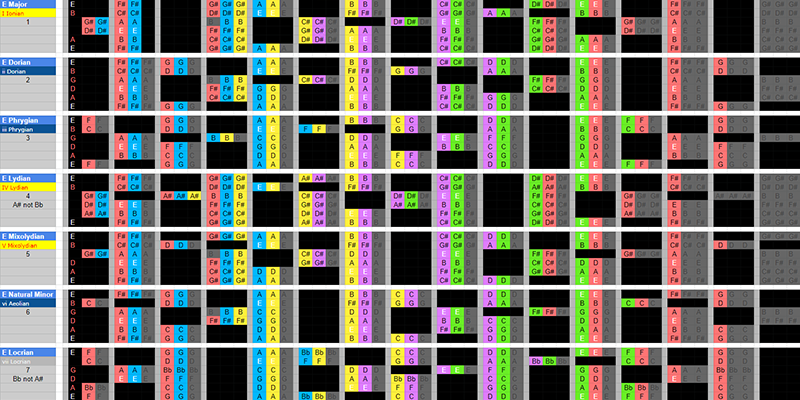
Next were the patterns. There are countless permutations of scales and keys, so it made sense to start with the basics - in this case the Major scale modes. The 7 patterns are divided into 5 colors, arranged logically from the underlying chord shapes in each section.

Shown here are differences between each of the 7 patterns. This set is based on the key of E, for a guitar with standard tuning. All patterns eventually loop at the 12th fret (notice the red pattern repeats at both sides).

Since each pattern can "slide" depending on which key it's in, the data is versatile and can be mapped to start anywhere. Any scale can be in any key. With dozens of scales, the variations are astronomical - so prioritizing the options was important in order to make realistic decisions.
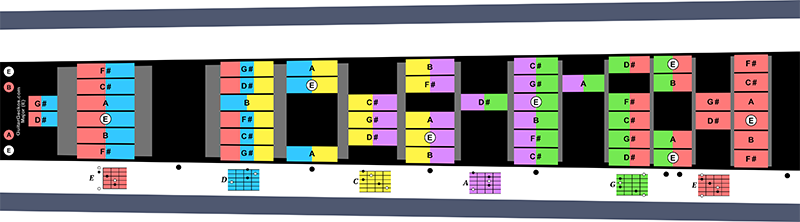
Here is the final pattern for printing, which is then laminated for durability and cut. For practical reasons, the final design of the physical product benefits by limiting the scope of what is offered.

Currently the patterns are produced with a cutting machine, which is slow and expensive. Offering every possible permutation in cut-out form is overload - for example, just 7 basic modes * 12 keys = 84 cut-out options. For a physical product, this is untenable - however, it's a perfect fit for a software solution...
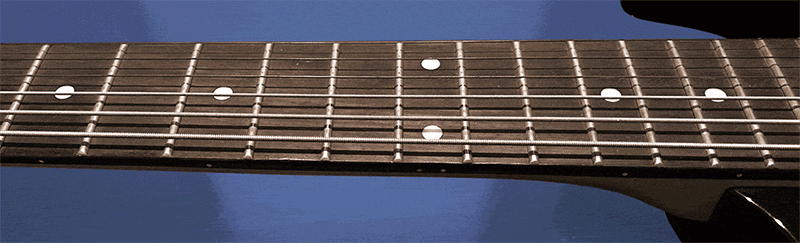
Which brings us full circle - back to the future version in AR. This will allow the user to pick from a much larger set of scales, and simply dial in the details - like which key they want to use, and what style overlay they would like to see (notes, finger positions, intervals). Additionally, a community of users could create and share their own content.